Having spent my career in reverse logistics, I’ve gained a deep appreciation for what happens after a consumer returns a product, something most rarely consider. When an item is returned, what happens next is complex. Is it restocked on the shelf to be resold? Perhaps it’s donated or liquidated through an auction site. Or, unfortunately, it might just end up in the trash. The truth is all of these scenarios are possible.
Managing a reverse logistics operation is a complex and dynamic task, requiring constant adaptation. Employees need to be trained, and employee churn is a constant challenge. Additionally, onboarding new clients and programs, each with unique requirements and ongoing changes, adds to the complexity. As a leader, you often become a change agent within the organization, where being agile and responsive to customer needs is essential to remain competitive.
Ultimately, reverse logistics is about more than just handling returns; it’s about navigating the intricate web of processes, people, and products to create value. However, there are reverse logistics challenges that businesses must overcome to achieve success.
One significant pain point is the continuous need to train new hires, whether due to company growth or employee churn. Training is an unavoidable cost, both in time and resources. It’s a necessary investment, but one that can strain operations if not managed efficiently.
How to improve reverse logistics? To mitigate these challenges, streamlining and simplifying processes is crucial. By refining workflows, you can minimize the learning curve for new employees, allowing them to become productive more quickly. But be careful not to oversimplify, as this can impact seasoned employees’ productivity. Additionally, having well-documented procedures and standardized training modules can reduce onboarding time and ensure consistency across the team.
Implementing an entirely new process adds another layer of complexity. It’s not just about training people on the new or existing process; it’s about ensuring that the transition is smooth and doesn’t disrupt ongoing operations. This requires careful planning and clear communication across the organization.
In essence, the key to managing reverse logistics challenges lies in making processes as intuitive and straightforward as possible. This approach not only reduces the burden of training but also empowers the team to adapt quickly to change, keeping the operation running smoothly despite inevitable turnover or growth.
Another significant pain point in reverse logistics is dealing with inflexible systems that demand extensive IT development and support. These systems can be a double-edged sword: while they may offer robust functionality, their rigidity often leads to a reluctance to change. This avoidance can push teams to create manual workarounds, which, in turn, increase the risk of errors and inefficiencies.
When systems are difficult to modify, implementing new processes or adapting to changing customer requirements can become a lengthy, resource-intensive endeavor. The extended timelines for such changes not only delay operational improvements but also drive-up costs. The longer it takes to implement a necessary change, the longer the organization is exposed to inefficiencies, compounding the problem.
The solution lies in advocating for more flexible, user-friendly systems that can adapt quickly to the evolving needs of the business. By reducing dependency on heavy IT support and enabling quicker, more agile responses to change, organizations can minimize reliance on manual processes, reduce errors, and shorten implementation timelines. This approach not only helps control costs but also fosters a culture of continuous improvement, ensuring that technology serves the business rather than the business serving the technology.
As an operations or IT leader focused on reducing costs, to achieve reverse logistics optimization, seek powerful tools that allow you to configure streamlined workflows at global, regional, customer, or process levels. This gives you full control over your operations and the data you collect. Break free from being forced to adapt your processes to fit rigid systems and design workflows that truly serve your business needs.
This level of flexibility means your IT systems will finally work for you, not the other way around. By empowering your team with tools to easily create and modify workflows, you reduce the need for costly IT development and support, speed up implementation timelines, and eliminate inefficiencies arising from manual workarounds. The result is a more agile, data-driven operation that can adapt quickly to changing demands, driving continuous improvement and cost savings across your organization.
In Summary, managing a reverse logistics operation is complex and requires constant adaptation to challenges like employee turnover and bringing on new clients or processes with varying needs. Leaders must navigate intricate processes to create value while dealing with change.
Streamlining workflows is crucial to minimize the learning curve for new employees and implementing new processes that ensure onboarding is efficient and consistent.
Another significant challenge is dealing with inflexible IT systems, which can lead to inefficiencies and increased costs when changes are needed. Advocating for more flexible, user-friendly systems can help organizations respond quickly to evolving needs, reducing reliance on manual workarounds and costly IT support.
By empowering teams with tools that enable easy modification of workflows, organizations can enhance agility, drive continuous improvement, and achieve cost savings, ensuring that technology supports the business effectively.
Contact us to learn more to find the right solution for your business.
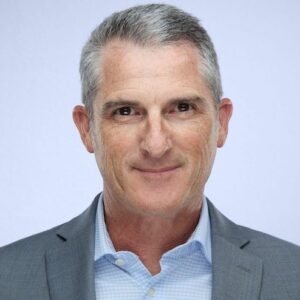
About the Author: Chris Bleess
Chris Bleess is Director of Business Development with Triage Partners. With over 25 years of experience in the wireless, telecommunications and consumer electronics industry, he has a deep understanding of the market dynamics, customer needs, and industry standards that shape the service lifecycle management sector.